Copying punches?
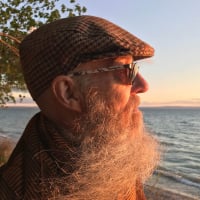
Nick Shinn
Posts: 2,291
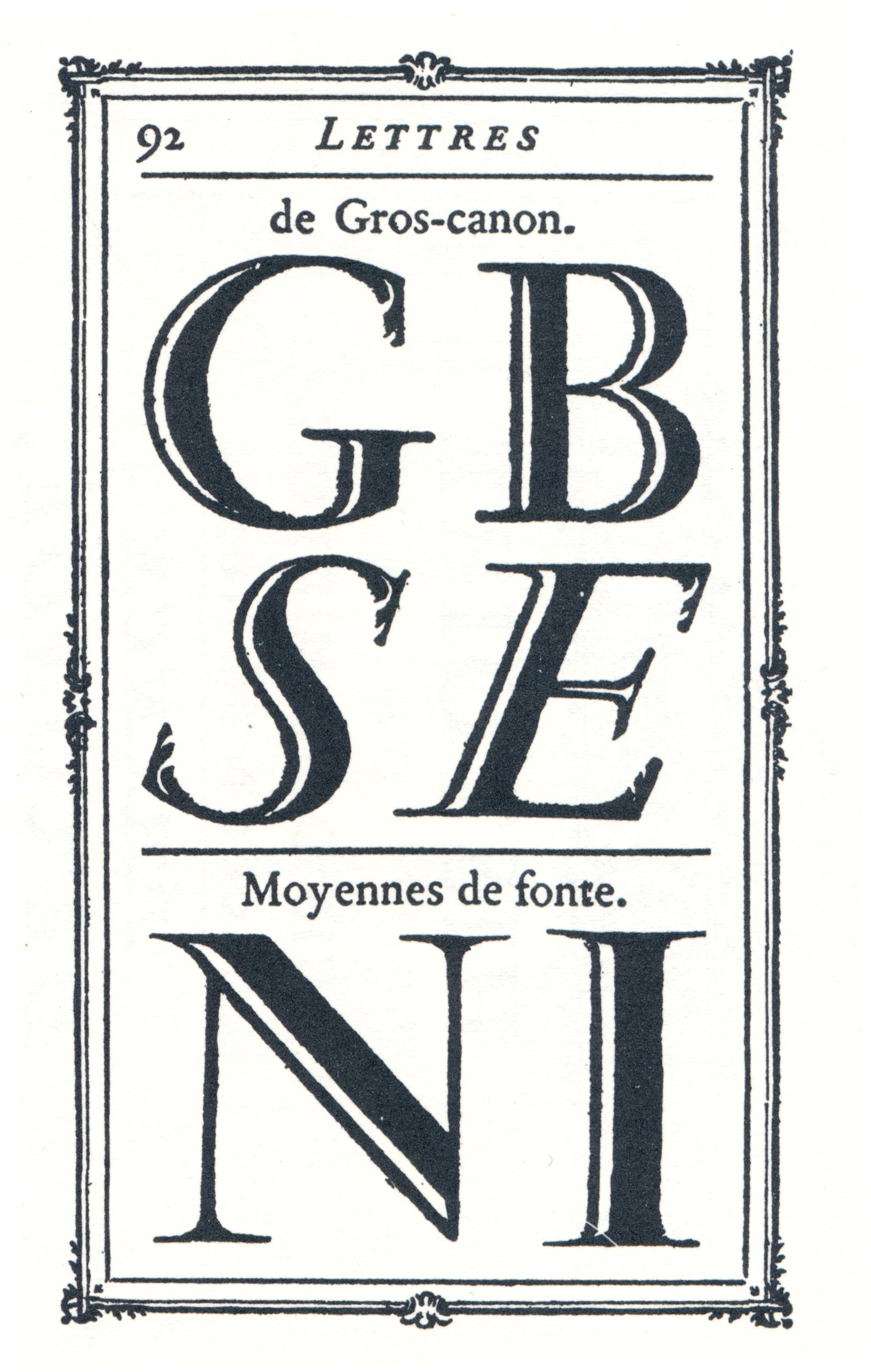
It seems possible that certain decorated types were made by digging away “highlights” on solid type punches.
But this would mean that those punches could no longer be used for making the solid style, only the highlight style.
That seems rather a waste.
Would it have been possible to make a steel copy of the solid punch, and then dig out the highlights on the copy?
Or some other method?
Above: an early example by Fournier le jeune, from 1765, scanned from Updike.
Tagged:
0
Comments
-
Early renaissance punchcutters in France made replicas of Italian type from looking at Italian books. And punchcutters all over the world copied broken punches to replace them. So I imagine it was trivial for them to copy a complete set of punches and then engrave decorations.2
-
But how did they do it so precisely?
What kind of mechanical process did they use?
Surely it can’t have been by eye.
Wouldn’t they have wanted to keep the solid-letter punches for use later, to make fresh matrices? (The matrices being of less durable material than the punches.)
This is a spread from Fry’s specimen of 1828.
0 -
I’m with James on this.0
-
I based my question on the description of the practice of modifying punches for decorative styles, by Rob Roy Kelly in American Wood Type: 1828-1900, page 22-24. (He talks about metal type in the book too.)
But he doesn’t discuss the issue that occurred to me, which was that once a punch had been “tooled”, it could no longer be used to make matrices of the un-decorated style.
But perhaps the already-punched, un-decorated matrices were, for the typefounder, durable enough to continue to cast type from. Or, perhaps the founders would produce many matrices for each letter, from the same punch, so they had a goodly supply of them, so it didn’t matter if the original punch had been tooled decoratively.0 -
Punchcutters worked at actual sizes and were very good at getting repetitive detail right. After the introduction of electrotyping in the 1840s, foundries did start editing soft-metal punches. But there is no evidence of any mechanical assistance in punchcutting prior to that.
The total number of strikes (unjustified matrices) that could be made from one steel punch is a random number. All punches will break eventually, after a certain number of strikes. Some punches broke the first time, others only on the 10th or 20th time. As James wrote, a punchcutter could recut a punch, and surely must have done this pretty regularly, while they were busy supplying different printers and founders with full sets of duplicate strikes. No punchcutter ever would have written a letter to a customer saying “sorry, I was going to send you a set of strikes from my Cicero Italic, but then the punch for my lowercase e broke, so this whole product is gone from my catalog forever. Woe is me!”4 -
After copying a couple of historical punches I can tell you it's not rocket science. It's fairly simple to use an existing punch or type to print with soot on translucent vellum or paper to trasfer the design to the face of a shank and then cut a new punch.Actually, if you read the chapter in Fournier's Manuel where he explains how to mirror the design of ornaments, you get to know how designs where reproduced and transferred to the punch.Below is (probably) Rädisch's copy of a Granjon's Ascendonica P, and you can see how a soot print was later engraved with a dry point and then cut.5
-
Not to discount the remarkable skill that 19th century punchcutters had at manually copying type, using the “soot image” tracing method or whatever, but it does seem a long-winded method of making decorated styles based on the exact outlines of solid type.
Your mention of stereotyping, Dan, is promising. Stereotyping existed before electrotyping, by Didot in 1800 at least, done with fine plaster, presumably.
If not mechanically copying punches, perhaps:- A sort of solid type was tooled with a decorative highlight (and kept as the “master”)
- A plaster mould (a “stereo”) was made from this
- Type was cast from the stereo
Plausible?0 -
>> But how did they do it so precisely?
>> What kind of mechanical process did they use?
>> Surely it can’t have been by eye.I think the problem is your main assumptions are wrong: If you have lead type as models you can cut very precise punch copies manually. And yes, it can be done by – a magnifier assisted - eye.Below is the replica punch I (a clumsy amateur) made from Gutenberg's B42 type in real size (4,2 mm). I assure you it's very very close to the original prints (actually the problem was which e in Gutenberg bible I was going to use as model).Below you can see the final soot test and the matrix I recently made with the punch. Soon I will cast some types.1 -
Walter Tracy recounts Rädisch "engraving a white line in the 36 and 48 point size of Lutetia capitals, under Van Krimpen's direction" to create Lutetia Open. I always took that to mean engraving the punches from the solid version directly.0
-
>> Walter Tracy recounts Rädisch "engraving a white line in the 36 and 48>> point size of Lutetia capitalsIn a few sources you can read that Rädisch cut Lutetia Open 36 and 48 directly on lead types and that the matrices were later produced using galvanic methods. What you won't find published anywhere is that Rädisch cut at least one steel punch of Lutetia Open 48 pt. How I know? Well, I own this punch and it's stamped with Rädisch's signature.Why there are also galvanic matrices? My theory is he started by cutting in his preferred way but was later told by J. Enschedé bosses to use a more modern / speedy method engraving lead types instead.Below, a couple of pictures of my Lutetia Open punch.
9 -
Nick Shinn said:
Your mention of stereotyping, Dan, is promising. Stereotyping existed before electrotyping, by Didot in 1800 at least, done with fine plaster, presumably.
If not mechanically copying punches, perhaps:- A sort of solid type was tooled with a decorative highlight (and kept as the “master”)
- A plaster mould (a “stereo”) was made from this
- Type was cast from the stereo
Plausible?
Also, if you edited your original punches with inlines or ornaments, you would not be able to make more duplicate strikes of the original design to sell to other founders (without remaking the original punch). All the methods that you are suggesting don’t make any economic sense with my reading of the historical record.1 -
> Before electrotyping, you needed steel punchesYou know, Dan, that softer alloys where usually employed with this method. Actually, I learned it from you
0 -
Right. A plaster “matrix” made from a tooled type “punch” would have had limited usability.
Thanks for your erudition, everybody!
One other thing that occurs to me: there were very few characters in these decorative fonts, which one is apt to forget in today’s practice of making huge fonts, so cutting fresh punches for a couple of dozen characters, no lower case etc., would not have been too onerous. And if any extra, rare characters were required, they could have been made on the fly by engraving straight onto plain roman type.
In conclusion, it’s likely that fresh punches were made for these early decorative styles, but following the proven design of solid roman letter forms.1 -
...or (equally or perhaps more likely), the old punches were used for these early decorative styles, with the knowledge that if solid punches were again required they could be remanufactured.1
-
Is it not possible to cast a new steel punch from old punch's impression?0
-
Steel couldn't be melt in Europe until the 18th century. When crucible steel was invented, it was possible to produce high quality carbon steel, the reason why Rädisch and others favored Huntsman steel from Sheffield. But dealing with molten steel is complicated: it requires very high temperatures and the stuff is thick, it's not easy to cast small objects with it.
7 -
I’m still inclined to believe that the Open version of the Fry style above was made by engraving the original solid punches, because of the "bad highlights” on B and M.
If the designer was making a fresh set of punches for a highlight style, why include the “inlines” on the wrong side?
In the fresh punch scenario, why go to the trouble of meticulously tracing and cutting the solid design, if that makes it so hard to produce a satisfactory highlight effect?
The designer must have been aware that the left stem of the M was not satisfactory, with the new highlight cramped and thin, but couldn’t remove or redraw the existing dug-out line on the right of the stem.0
Categories
- All Categories
- 46 Introductions
- 3.9K Typeface Design
- 481 Type Design Critiques
- 558 Type Design Software
- 1.1K Type Design Technique & Theory
- 648 Type Business
- 841 Font Technology
- 29 Punchcutting
- 515 Typography
- 119 Type Education
- 320 Type History
- 76 Type Resources
- 110 Lettering and Calligraphy
- 31 Lettering Critiques
- 79 Lettering Technique & Theory
- 540 Announcements
- 88 Events
- 112 Job Postings
- 168 Type Releases
- 171 Miscellaneous News
- 275 About TypeDrawers
- 53 TypeDrawers Announcements
- 120 Suggestions and Bug Reports