Old fashion petrol blowtorches for heat treatment

Ramiro Espinoza
Posts: 839
I was a bit fed up with my propane blowtorch because it loses pressure quite quickly and stop delivering the very hot flame necessary to heat the punches to the 'cherry red' point. I don't like canisters and disposable cartridges (I still write with an indestructible Parker 51) so I decided to try the notoriously unsafe petrol blowtorches as recommended by Paul Koch in his Dolphin's article.
I purchased a mint 'BAT' blowtorch manufactured in the German Democratic Republic
and after reading all the safety recommendation published at: http://www.blotorches.com/horror.html I gave it a try.
I filled the container to 3/4 of its volumen with benzine (wasbenzine), followed the starting protocol with alcohol (less smoke) and could make it deliver a very hot a powerful blue flame. Then I took a blank punch to the glowing red point in about 3, 4 minutes. Faster and more evenly than with the propane blowtorch. I liked it and I will continue using it.
So, provided you use a petrol blowtorch in good condition, have a lot of care handling a volatile fuel and operate it with proper knowledge of the tool; it's a very useful device for hardening punches.
Please if you decide to try one of these, please learn well how to operate it before doing anything: http://www.blotorches.com/startshu/startshu.html
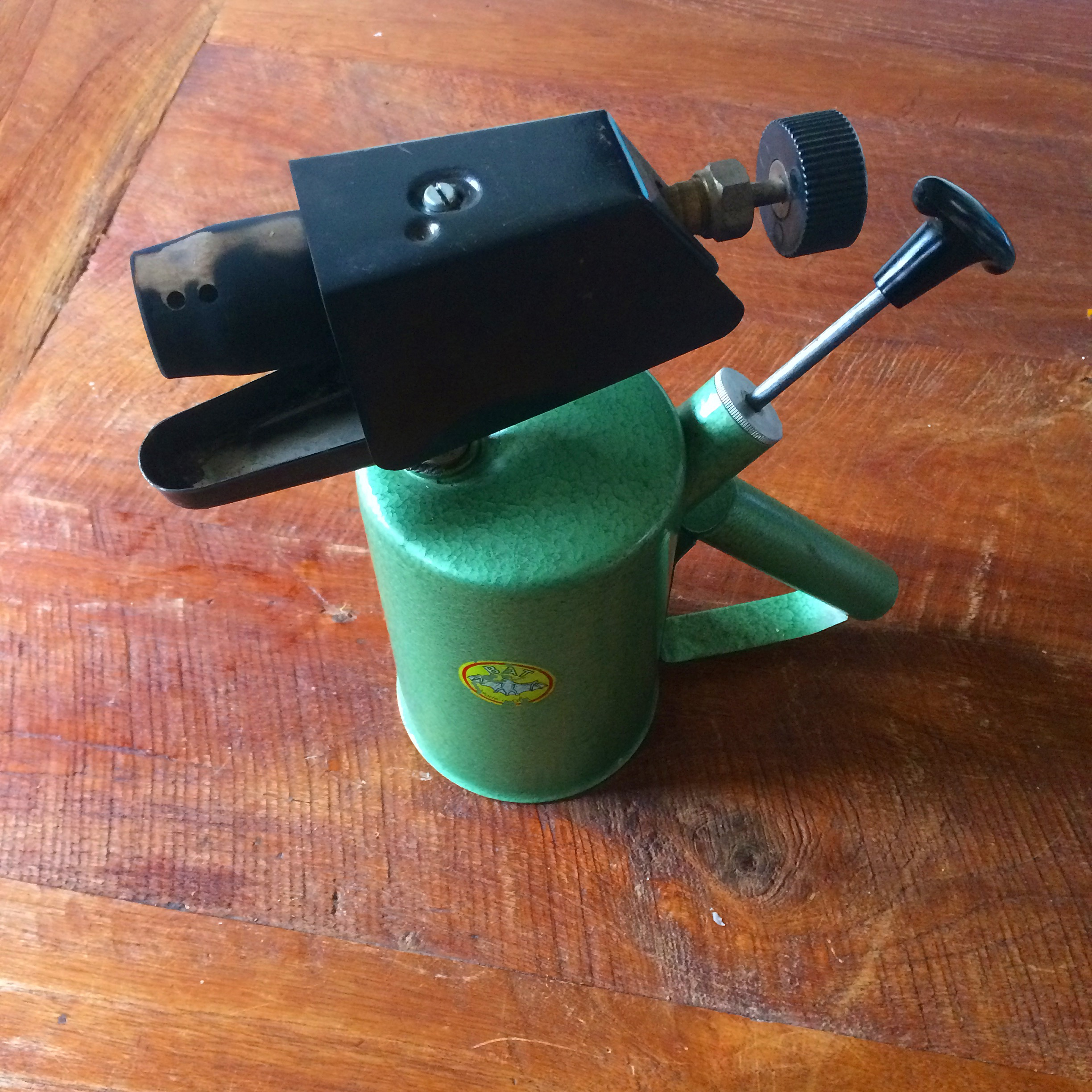
I purchased a mint 'BAT' blowtorch manufactured in the German Democratic Republic

I filled the container to 3/4 of its volumen with benzine (wasbenzine), followed the starting protocol with alcohol (less smoke) and could make it deliver a very hot a powerful blue flame. Then I took a blank punch to the glowing red point in about 3, 4 minutes. Faster and more evenly than with the propane blowtorch. I liked it and I will continue using it.
So, provided you use a petrol blowtorch in good condition, have a lot of care handling a volatile fuel and operate it with proper knowledge of the tool; it's a very useful device for hardening punches.
Please if you decide to try one of these, please learn well how to operate it before doing anything: http://www.blotorches.com/startshu/startshu.html
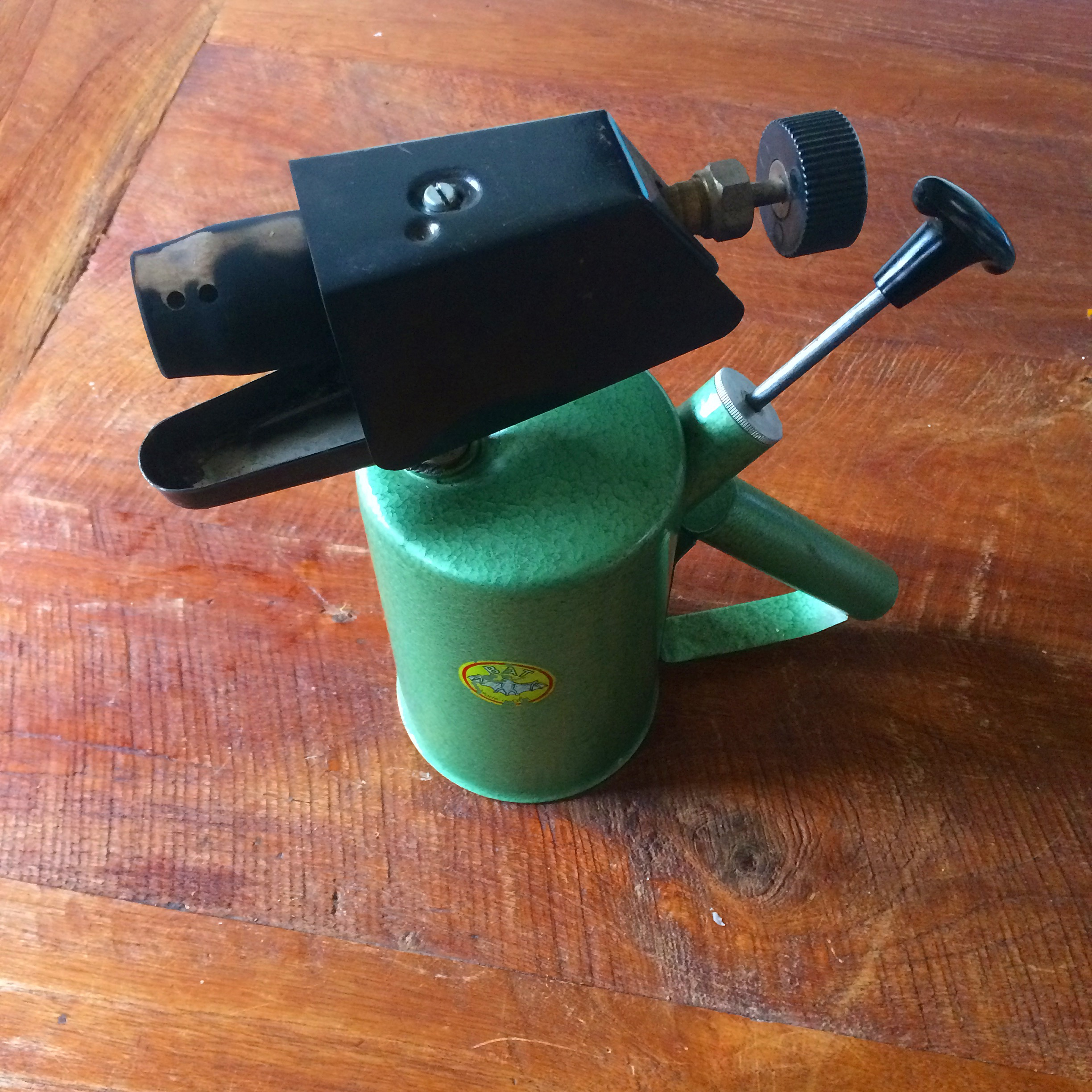
1
Comments
-
Hmmm,
i would stick to gas. Using a large gas bottle like roofers do. Either Butane or propane. The also come in smaller sizes.
Does anybody have an idea on where, how and what kind of oven for the hardening?
kind regards
Patrick
0 -
I guess a small hardening electric furnace should not be very difficult to make with the resistance of an electric stove and refractory ceramic casing. The casing can be cast with a 50/50 mix of sand and plaster. Yes, it's only for DIY fans, but completely doable.1
-
Patrick I have been looking at this and there appears to be overlap in the interests of punchcutters and knife makers. Here are some typical heat treat ovens for hardening: https://usaknifemaker.com/knife-making-machinery.html
0 -
The annealing oven is a idea of making the hardening of steel into an exact science and as Patrick and I know this is not the case, there were problems with the oven in the Imprimerie National and getting it right can be trial and error, the major worry is the damaging the face of the punch when using a blow torch, but with a bit of practice this can be avoided, the thing is to get an even temperature throughout the punch before quenching into water or oil, then the test after to see if you have got it right is to run a file on the punch, it should glide off the punch. Now, as to regards the quenching of your punch, if your steel specifies water or oil, then this what you use, in engineering there are specific oils, in my early years we used Whale oil, this had the correct viscosity but did stink when plunging the metal, and I doubt if available anymore, nowadays quenching oil is available and has a viscosity of a hydraulic oil (don't use this), getting this right can mean your punch will be correctly tempered and should avoid splitting, (this bit is in more simplified terms) the reason for this quenching is getting the steel to cool at the correct speed, the molecules then stick together properly, the amount of Carbon in your steel can effect this, so if the steel cools too quick it can cause these molecules not to stick together properly, thus your steel can split or crack.
Just something to tell; many years ago as a budding Scientist (where did I go wrong?)we experimented with Carbon steel, heating it then plunging it into liquid Nitrogen, then hitting it causes it to shatter into shards, just something we did to prove that the steel molecules were not sticking together.
2 -
The most difficult part in my opinion is not hardening, but tempering punches to the right point. And even more complicated than tempering the punches is the matter of weather or not to temper counterpunches. Paul Koch does not say much about it, except that he did temper counterpunches but, according to my experience, small counterpunches should not be tempered at all and bigger one can be tempered but only very lightly (100-150 C?). Remember that in the case of counterpunches you are striking steel, not copper. The construction of counterpunches should also be sturdier with less steep sides.0
-
A little video of my benzine blowtorch being used to harden a counterpunch: https://www.flickr.com/photos/retype/40378061335/in/dateposted/0
Categories
- All Categories
- 46 Introductions
- 3.9K Typeface Design
- 481 Type Design Critiques
- 558 Type Design Software
- 1.1K Type Design Technique & Theory
- 648 Type Business
- 841 Font Technology
- 29 Punchcutting
- 515 Typography
- 119 Type Education
- 320 Type History
- 76 Type Resources
- 110 Lettering and Calligraphy
- 31 Lettering Critiques
- 79 Lettering Technique & Theory
- 540 Announcements
- 88 Events
- 112 Job Postings
- 168 Type Releases
- 171 Miscellaneous News
- 275 About TypeDrawers
- 53 TypeDrawers Announcements
- 120 Suggestions and Bug Reports