Type alloy is too brittle for testing counterpunches

Ramiro Espinoza
Posts: 839
As several articles and books mention type alloy as a good medium to test the impression of counterpunches, I also tried to use it. After striking several metal types on the side (and shuttering all of them) I arrived to the conclusion that type metal is too brittle for this purpose. I think it's better to use pure lead instead.
In the end I managed to strike and not break a type alloy spacer plate, but it was difficult. So guys, use lead. I will try also an aluminum plate, I think it should work.
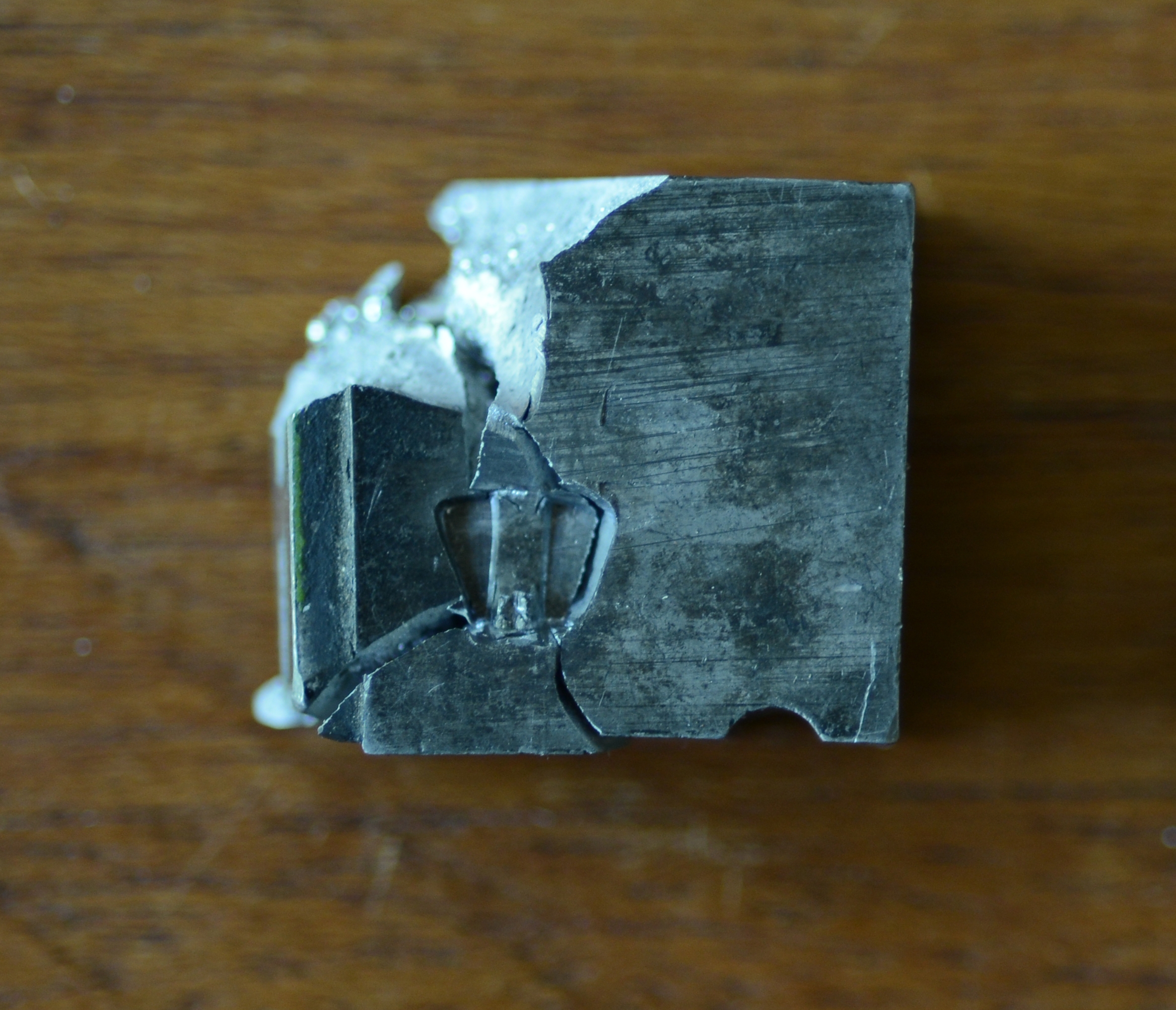
In the end I managed to strike and not break a type alloy spacer plate, but it was difficult. So guys, use lead. I will try also an aluminum plate, I think it should work.
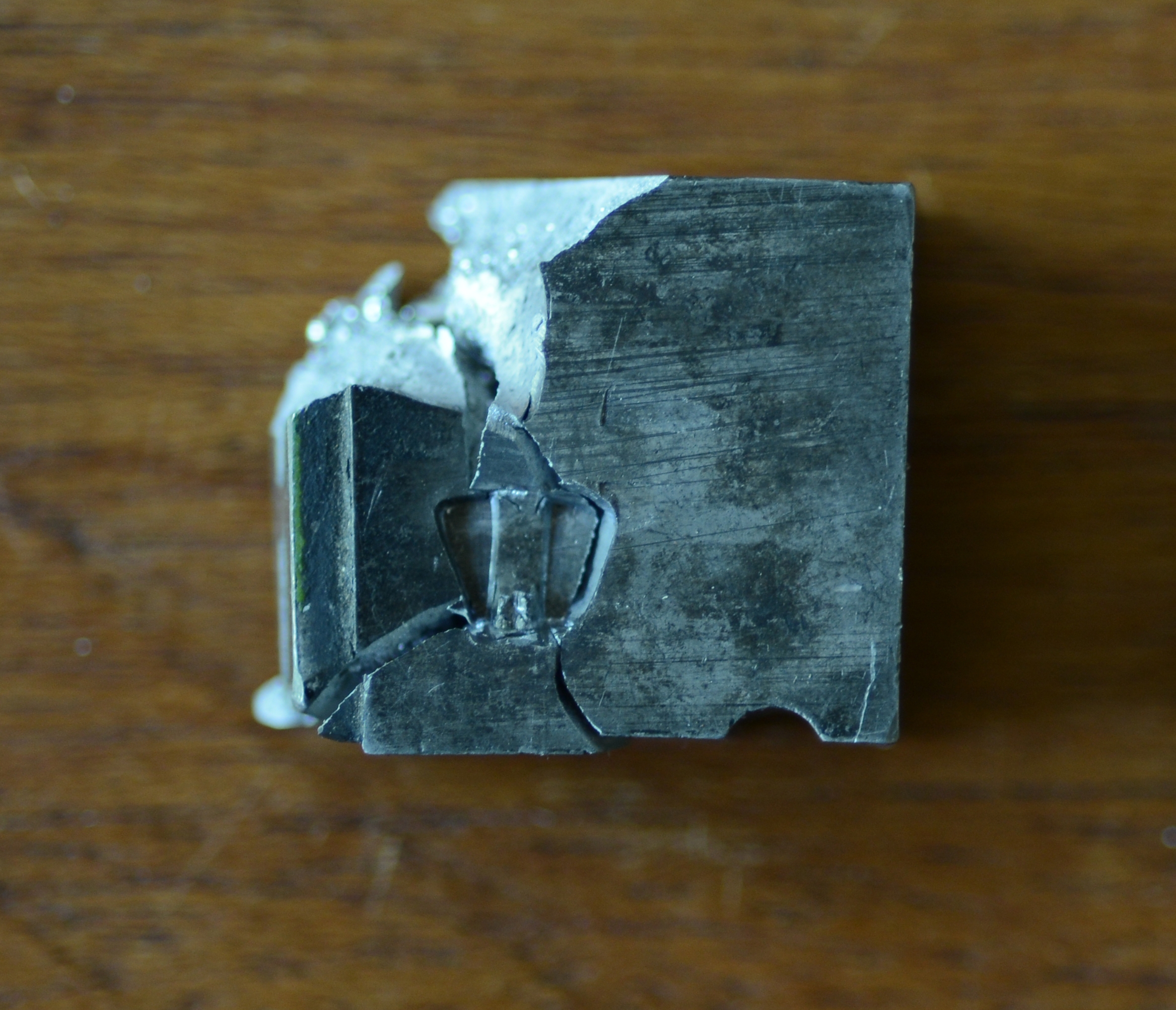
Tagged:
0
Comments
-
Not all alloys are equal of course... Hotmetal alloy for example is junk. Pure lead? Isn't that even further removed than what actual punchcutters used?
0 -
The punchcutter (specifically) only needs a soft metal such as lead for proofing counterpunches. You can't proof a counterpunch with a smoke proof, because the smoke proof tells you what the end of the punch looks like. With a counterpunch, what finally prints is a cross-section of the punch at counter-depth-of-drive distance up from the end. In his 2016 Wells College class, Stan Nelson specifically recommended against using typemetal for this, because it is too brittle. (Ramiro demonstrated this quite well in the photograph above, which, while documenting a minor setback in his process also qualifies as one of the finest teaching photographs ever taken - thanks for sharing it!) Stan used instead a bar of soft lead (no particular alloy - there are many - but generally mostly lead and quite soft). This took the counterpunch impressions well, and when "used up" could be flattened out again for re-use (or recast). Here's a photograph of one of Stan's counterpunch-proofing lead blocks:
In the USA, rotometals.com is a convenient supplier of many nonferrous alloys.
A matrix justifier will have need of typemetal alloy, but I wouldn't think that the particular alloy is important for this purpose. In justifying, all you're doing is casting test types which will be examined visually and possibly proof printed.
Even in production typecasting, it all depends on what you're making and, as importantly, how you're using it. If you consider volume of production, then Linotype, Ludlow, stereotype, and various Monotype composition casting alloys produced very nearly all of the printed material that people saw for the first half of the 20th century. And, again in terms of volume (of punched matrices certainly, and probably of punches), the Mergenthaler Linotype Company was the most prolific punchcutter in the history of printing. Barring contamination (e.g., with zinc), every typemetal has its use.
As an aside, there was one historical situation where the punchcutter (or at least the matrix striker) did use lead. But it was a process employed in the 18th century, then forgotten, and then rediscovered (by Stan Nelson with James Mosley). There is an account of it on Mosley's blog, but it has also finally been published:
Mosley, James. "Big Brass Matrices: A Mystery Resolved?" Journal of the Printing Historical Society. New Series, No. 23 (Autumn 2015): 45-48.
(As an aside, if you don't have this number of the PHS Journal, get it while you still can. It is devoted to Mosley's work, and as such is by definition one of the most important works you can have in your library. It also contains Mosley's translation of the section on the hand mold from Jaugeon's unpublished manuscript.)
The process addressed the problem of making really big type in metal; it was one of several very different solutions. Basically, in this method, they cut a very large punch in steel and then drove it into a lead blank to make a lead strike. (Driving a punch of this size into a copper alloy would require punch presses larger than those which existed in the 18th century; English Monotype only started doing this in the mid-20th century.) Then they would sand-cast a *brass* (not copper) matrix using this lead strike as a mold. This was a bit rough, so the final step was to re-drive the steel punch into the cast-brass matrix to use the punch to "clean up" the casting cavity of the matrix.
Stan, being a superbly practical theoretician, not only figured this out from the (scant) surviving evidence but then demonstrated it by doing it. I can't remember the punch size here - it is intended for something on the order of a 60 pt or 72 pt body, but it's HUGE).
I took the photo above at the ATF 2010 conference in Piqua, Ohio. Below is a 2016 photo of the same materials (sans the punch) which shows the cast type on its side with the jet still attached. Jet breaking on type of this size is non-trivial.
2 -
I just checked Stan's handouts for the 2016 Wells class, and he does in fact say "pure lead" for proofing counterpunches. I don't suppose that means it has to be chemically pure, of course! But definitely soft.1
-
Today I made some tests and it's very simple to use a piece of modelling clay / plasticine to check the counterpunches' shape.0
Categories
- All Categories
- 46 Introductions
- 3.9K Typeface Design
- 481 Type Design Critiques
- 558 Type Design Software
- 1.1K Type Design Technique & Theory
- 648 Type Business
- 841 Font Technology
- 29 Punchcutting
- 515 Typography
- 119 Type Education
- 320 Type History
- 76 Type Resources
- 110 Lettering and Calligraphy
- 31 Lettering Critiques
- 79 Lettering Technique & Theory
- 540 Announcements
- 88 Events
- 112 Job Postings
- 168 Type Releases
- 171 Miscellaneous News
- 275 About TypeDrawers
- 53 TypeDrawers Announcements
- 120 Suggestions and Bug Reports